Before we dive into the topic of proofing and gauging, it’s useful to establish some background and definitions; while they may be familiar to you as experienced distillers, these will form the vocabulary for this article. These definitions and regulations primarily apply to United States-based producers, though there are comparable terms and guidelines in most jurisdictions. Additionally, proofing and gauging are complex topics; I’ve chosen to ignore some of the finer points for the sake of brevity. Now, let’s begin!
Proofing is the act of determining the alcoholic strength of spirits. Proof is expressed in degrees (e.g. 90°pf, which is equivalent to 45% ABV). “Proofing down” is the act of adding water to spirits that have been proofed to reach a target alcoholic strength. “Proof” and “proofing down” are sometimes used interchangeably – stay vigilant to avoid confusion.
Weighing is the legally-required method to determine the quantity of liquid in a tank or container for most craft producers. You should record the empty (tare) weights of all containers you use for spirits so that you can subtract it from your observed (total) weight to determine the net weight of spirit, and therefore tank content. Weight must be measured in pounds and then converted to volume (gallons) using the TTB Gauging Manual.
Gauging is the act of determining the total alcohol quantity in a given tank or container. A gauge is expressed in proof gallon terms. You must have a measure of the proof and the weight in order to compute your gauge. In simple terms, Proof + Weight = Gauge.
Here’s a real-world example: Let’s say that you receive a tote of Grain Neutral Spirit and you wish to gauge it, as required by 27 CFR.
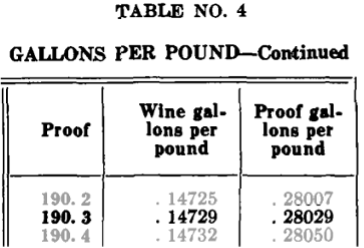
First, measurements. You weigh it on a floor scale and observe a weight of 1951 lb. The paperwork accompanying the spirit indicates that the tare weight of the tote is 125 lb, so the net weight is 1826 lb. Now, you can grab a sample of product from the tote and proof it using one of the approved methods (e.g. hydrometer & thermometer). In this case, your proofing results indicate 190.3°pf.
These two values are all that you need to compute your gauge. To determine the proof gallons in your 1826 lb of 190.3°pf spirit, refer to Gauging Manual Table 4 and look up your proof to find proof gallons per pound. Here, you can see that 190.3°pf spirit has 0.28029 proof gallons per pound. Then it’s just simple multiplication: 0.28029 * 1826 lb = 511.81 proof gallons. For extra credit, you can also determine the wine gallons (ordinary gallons) of product using the conversion factor for 190.3°pf (0.14729 gal/lb): 0.14729 * 1826 lb = 268.95 wine gallons.
Historical background
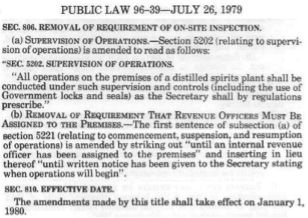
Up until 1980 – when deregulation hit the industry – gauging was only performed by US government agents. Spirit collection tanks had locks, with keys held only by agents. A proprietor couldn’t even touch his own distillate until unlocked and gauged by the resident agent.But, with the stroke of a pen, gauging responsibility shifted from federal agents to DSP proprietors (Distilled Spirits Tax Revision Act of 1979). This would have been a great moment for the US Government to harmonize with the rest of the world and begin measuring proof at 20C instead of 60F. Instead, legislators left the Gauging Manual essentially unchanged from its original publication by government chemists in 1938. If you’re ever wondering why the manual & methods seem obtuse, it’s because they had to be usable by candlelight with rudimentary tools and a slide rule.
Does all this seem like… a lot?
That’s because it is! Humans aren’t computers, and software is designed to crunch numbers: why not leverage Distillery Management Software to do the heavy lifting for you when it comes to proofing and gauging? DISTILL x 5 and Whiskey Systems include built-in calculations from the Gauging Manual to automatically convert between weight, volume, and proof gallons or LAA. You just enter your measurements, and all the data gets computed, collected, stored and formatted for federal reporting. How easy is that?
If you’re still overwhelmed, reach out to us here to schedule time with our consultant and take your operations to the next level.

Tyler Derheim is Fx5’s in-house consultant, using his expertise to help distilleries of all sizes make it easier to make great things. Tyler first entered the regulated beverage industry in 2010, when he started working harvest and crush at a midsize winery in Slovenia. After returning to California in 2017 he joined a startup DSP, with responsibilities for formulation, production, compliance, lab services, and more. In 18 months, he led the DSP from mason jars and buckets to tankers and trailers, then moved into a freelance consulting role, helping distilleries of all sizes with every aspect of production, operations, and compliance. A long-time Fx5 user, Tyler brings a wealth of experience unmatched in the industry.